Time
1.1.2024–31.12.2025
Project coordinator
Åbo Akademi University
Funded by
Budget
701 413 euros
Åbo Akademi University’s part of the budget
701 413 euros (100%)
Steelmaking contributes by 7% to Finland’s fossil CO2 emissions, so to become carbon neutral the steelmaking processes must be converted to rely on renewable reductants and energy sources.
The research of this application develops digital tools for addressing three important challenges in the green transition of the steel industry.
The first challenge is how to realize a hydrogen-based reduction of iron ores instead of the coal-based blast furnace-basic oxygen furnace route applied largely today. Iron ore reduction by gas-solid reactions in a direct reduction (DR) shaft furnace using hydrogen as the reductant is not yet industrially proven, so numerical models of a DR furnace will be developed and applied to find ways of operating the process efficiently. A 2-D static model will provide a detailed view of the internal conditions to guarantee a proper metallization of the burden and to minimize the energy demand. A one-dimensional dynamic model will be developed to assess the potential of flexible operation, adapting the production to market conditions (e.g., steel demand and power price).
The second part tackles the transition of steel reheating furnaces to carbon-lean or -free operation by developing digital tools prediction temperature fields and NOx emissions. A model for simulation of the temperature distributions in the slabs will also be developed, by which the thermal conditions of the furnace are optimized to fulfil the slab heating requirements without excessive use of energy.
The third part focuses on the changes of the energy flows in the steel plant under transition, and the opportunities and challenges faced when the fossil fuels and raw materials are abandoned which simultaneously stops the generation of by-product gases. A numerical tool for enhancing the energy efficiency of the new steel plant will be developed, also exploring the potential of using obsolete unit processes as local energy storages.
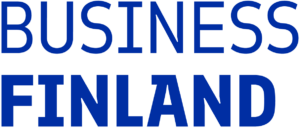
Contact us
Henrik Saxén (Principal Investigator)
Professor
Laboratory of Process and Systems Engineering
Tel. +358 405443301